【6回】接着剤の品質管理
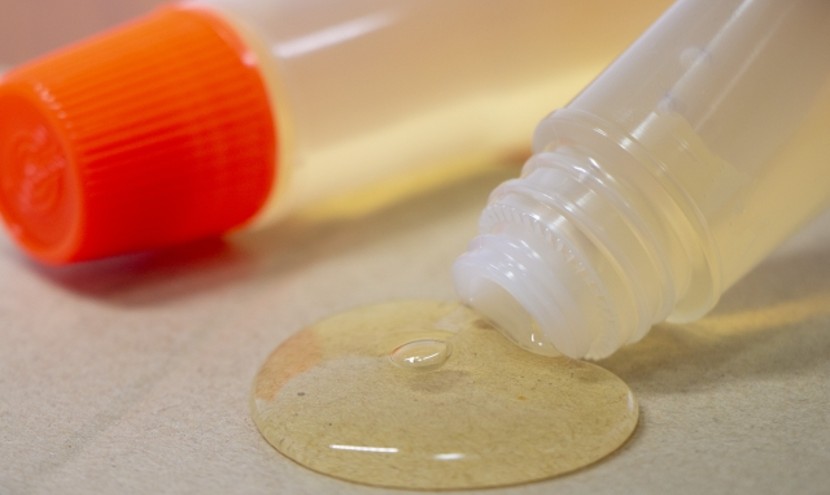
粘度は、その物質の特性を表す重要な指標の1つとなっています。
接着剤工業では製品開発や品質管理に早くから粘度を活用しており、その標準化を図ってきました。
結果、レオロジー特性の研究が進展するに伴って、多様化・高度化した用途に対応する接着剤がさまざまに実現しています。
これら接着剤は、実際の作業条件に合わせた適切な性質(非ニュートン性、チクソトロピー、降伏値 等)が与えられています。
接着剤塗布時の作業性や仕上がりの品質(接着強さ、滑らかさ(レベリング)、タレない 等)は、いわば、レオロジー特性によってコントロールが可能となっているのです。
今回は接着剤の性能評価について、粘度計測との関わりからまとめてみます。
接着剤の作業性とその評価
接着剤をはじめ、塗料やコーティング材など現在の工業製品製造に欠かせないこれら素材について、粘度測定を行う目的は大きくは次のように集約できます。
(1)流動挙動は製品の均一性と品質の間接的な物差しとなる。
(2)物質の特性化・差別化に最も感度のよい方法である(分子量・分子量分布・粒度・粒度分布・濃度・構造の度合いなど)。
(3)作業性の直接評価ができる(塗布性・ポンプ輸送時の動力・塗膜厚管理・タレ性・レベリング性など)。
接着剤は硬化後に所定の機能を果たせることが前提ですが、それと同時に、上記(3)にある作業性(の良さ)も非常に重要な商品特性となっています。
ビル建築などを想定すると分かり易いと思いますが、接着剤を使用する箇所・量は非常に多く、製品が扱いやすい特性であることは工期や工程に大きく関わってきます。
特にタレ性やレベリング性は、作業性の良さを評価する重要なファクターです。
ただし両者は、「レベリングしやすい=タレ易い」というトレードオフの関係にあり、そのちょうど良い設定を材料メーカ各社が競っています。
作業性についてもう少し具体的に見てみましょう。
実際の作業現場では、「壁面塗布でタレる」「塗布のくし目後が残る」「刷毛からタレる」「のびが悪く疲れる」「カートリッジから出にくい」等が挙げられています。
こうしたクレームは、塗布の方法・作業目的・用途において、それぞれ相反した性能が要求されていることに起因しています。
従って、より適した接着剤を選択するために、使用に際してその性能評価が必須となります。
しかし、塗布性の評価方法は種々ありますがいずれも科学的な定量性確保に乏しく、経験に頼った試行錯誤の方法で行われることが多いのが現状です。
そこで業界においても、標準的な評価手法を確立する試みが進められています。
規格化が進められているプラグフォーマー法
現在、規格化(FDIS 14678)が進められている品質の測定方法に、プラグフォーマー試験機を用いたタレ試験(sagging)があります。
これは試験機凹部に被験対象の接着剤を充填し、表面を平滑にした後に試験機を垂直に立て、凹部にある接着剤を押し出し(凹部の底は稼働構造になっています)、垂れる距離とその時間を測定します。
また、流動性が大きい試料では、押し出さないで凹部から垂れてくる距離を測定します。
プラグフォーマー法は、以下のような特長を持っています。
(1)流動性の大きい試料から建築用フロア仕上材、シーリング剤まで、幅広く接着剤の垂れ性を評価できる。
(2)サンプルセッティング(プラグヘの試料充填)に個人差が少ない。
(3)繰作性が良く簡便である。
以上の点から、接着剤一般のタレ性評価方法としてデータが参照されるようになっています。
しかし、いかにサンプルセッティングが簡易だとはいえ、複雑な物性を持つ高分子構造体、例えば接着剤に一般的なチキソトロピー性材では、事前の状態調整(温度、攪拌等の負荷)によって大きな差が生じることが明らかになっています。
簡単に言えば、どういう条件でテストするかによって、タレ具合が大きく変化してしまうということです。
このように、事前の状態調整と試験者の充填方法に大きく依存してしまう点において、プラグフォーマー法による計測も必ずしも定量的手法と言い難い面を持っています。
製品の物性や品質評価には、定量的、科学的で、試験者によって誤差の出にくい測定を行うことがやはり大事なってきます。
その手段の1つが、直接的にタレを計測するのではなく、接着剤の粘度計測を活用してその特性を評価することなのです。
結局、最適な試験方法とは?
多くの接着剤は前述のように非ニュートン性の材質であり、粘度はずり速度によって大きく変化します。
そのため、作業性(レベリングやタレ性)を評価するときには、降伏値や低いずり速度での粘度挙動を測定することが重要になってきます。
簡易測定器具によるプラグフォーマー法では、そうした条件設定を確実にすることが難しいのは前述の通りですが、一方、粘度測定では、粘度計で定量的にずり負荷を与えてから粘度測定を実施することは極めて容易です。
少し具体的に見てみましょう。
プラグフォーマー法によるタレ量と粘度特性値の1つである非ニュートン係数μ(3゜コーンロータの0.5rpmの粘度に相当)に相関することが種々の実験結果から明らかになっています。
これは、一般的な粘度計を使った0.5rpmの一点測定の結果から、目的とする材料のタレ特性が判断出来ることを意味します。
さまざまな手順を踏むといった面倒な試験をこなさなくとも、粘度計測という定量的かつ簡便な手法で、作業性や品質における信頼性の高いが評価が可能となります。
しかしながら、接着剤は複雑な高分子構造の複合製品であり、素材のレオロジー特性が製品へと反映されています。
例えば、温度やずり速度に大きく依存するチクソトロピー性に対応した評価を行うには、やはり”粘度のプロ”の測定ノウハウが必要となるケースも出てきます。
当社では、長年にわたり蓄積してきました様々なデータや経験を元に、最適なサポートをご提供することが可能です。
接着剤における品質管理や研究において、粘度計測をぜひご活用ください。